Automation and Equipments
Through our extensive knowledge we develop and manufacture machines with the highest degree of automation. However, we also use our knowledge from the various fields of nonferrous metal processing to design complete new production plants.
Example 1: Complete equipment for profile production
The plant consists of an inductive billet heating device, an extrusion press and the profile outlet. The transport of the billets between the feeding stations, the billet heating device and the billet loader is handled by a gantry robot. On the extrusion press, both the direct and the indirect process method can be used. The system is supplemented by a press disc- and press residual loader. In addition a profile shear allows the cutting of partial lengths in the profile outlet. The profile outlet has a puller that guides the profile with traction control. A large cross conveyor supports the profile until complete cooling down. The finished rods are placed in a belt recess.
Example 2: Complete equipment for wire production
In order to be able to produce wire, our equipment consists of a continuous casting machine, which is fed by two furnaces with feeding equipment. Afterwards the continuously casted billets are fed to the extrusion press by the help of a gantry robot. Billets can be added or removed via an intermediate inlet/ outlet. Inline with the extrusion press is a spooling machine, which winds up the wire made out of the pressed billets. The equipment can be extended by a flux feeding system in order to produce filled solder wire. Optionally, several wire drawing machines can be installed inline instead of the spooler.
Example 3: Complete equipment for ingots production
The equipment consists of a ingot casting line, a cooling line, a casting line for ingots pallets, a stacking system, a packing system and a pallet storage system. The core of the equipment is the ingot casting line and the subsequent cooling section. The rear part of the equipment realises a fully automated palleting and packaging of the ingots. Here the ingots are aligned, collected, sorted and packed. The resulting packages are weighed and marked in the pallet storage system. Afterwards the finished packages can be removed with the truck.
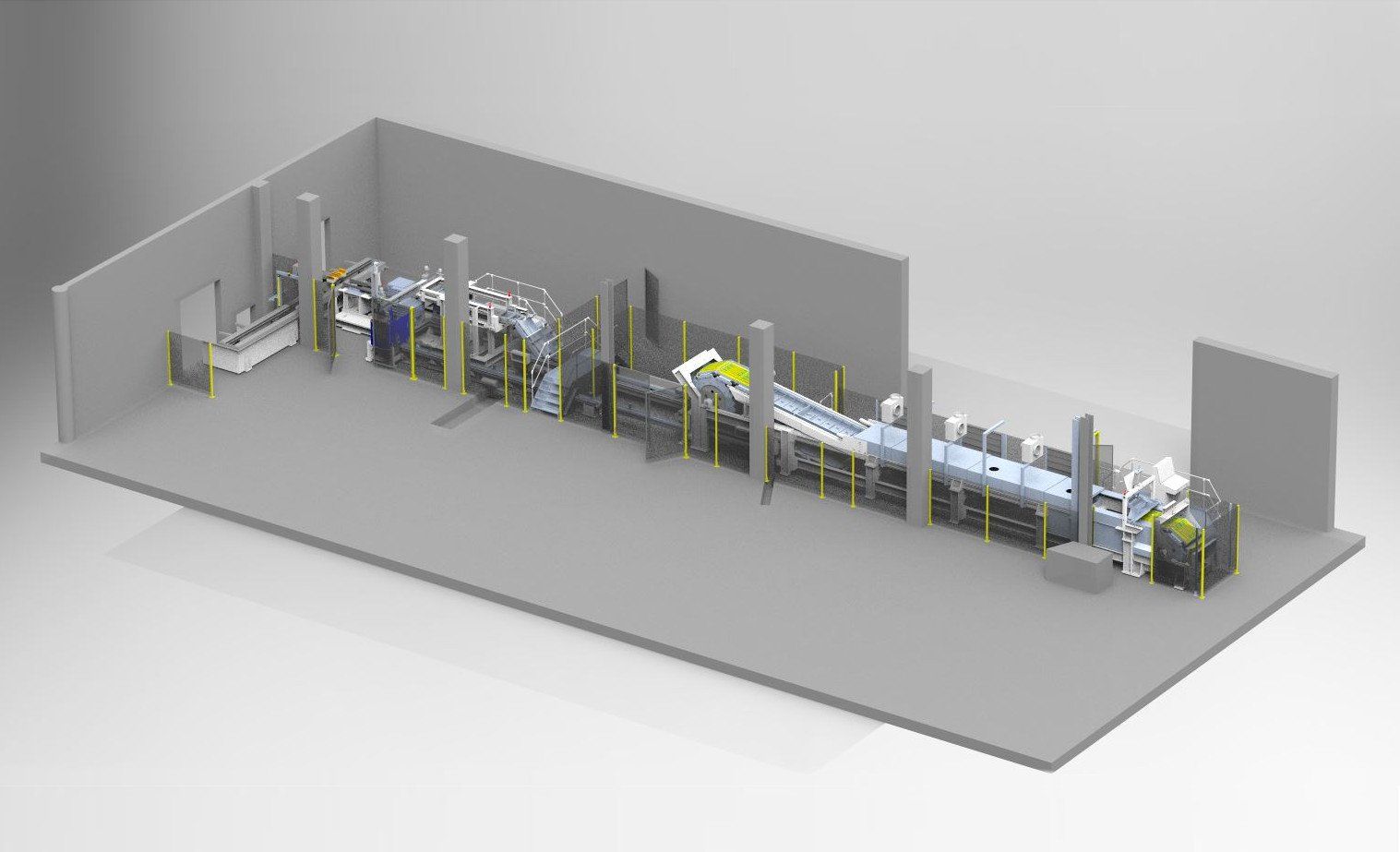
Process data acquisition
The data collected by the machine control system is transferred via a port to the onsite computer. Using the software supplied by us, this data is systematically recorded and saved. On customer request, we also offer process data storage and visualisation. The evaluation of the process data can be done, for example, with the usual office software.